Checking Out the Different Methods and Technologies Behind Plastic Extrusion
The realm of plastic extrusion is a blend of precision, technology, and modern technology, pivotal to numerous sectors worldwide - plastic extrusion. Advanced equipment, electronic controls, and a range of materials merge in this complex process, generating high-grade, sturdy products. As the industry advances, a change towards lasting products and intelligent equipment appears. The complying with discussion will certainly drop light on these innovations and techniques, while additionally meaning the exciting future leads of this critical manufacturing process.
Comprehending the Essentials of Plastic Extrusion
The process of plastic extrusion, usually hailed as a cornerstone in the world of production, forms the bedrock of this discussion. Fundamentally, plastic extrusion is a high-volume manufacturing process in which raw plastic product is thawed and formed into a constant account. It's a method widely employed for producing items with a constant cross-sectional account, such as pipes, window structures, and climate stripping. The process begins with feeding plastic products, usually in the type of pellets, into a warmed barrel. There, it is combined and warmed until it becomes molten. The molten plastic is then required with a die, forming it right into the wanted kind as it hardens and cools.
The Function of Different Materials in Plastic Extrusion
While plastic extrusion is a frequently made use of method in production, the materials used in this process greatly affect its final result. Various types of plastics, such as pvc, polyethylene, and abdominal muscle, each lend unique buildings to the end item. Makers must thoroughly take into consideration the residential properties of the product to enhance the extrusion process.
Strategies Utilized in the Plastic Extrusion Refine
The plastic extrusion process includes different methods that are critical to its operation and effectiveness (plastic extrusion). The discussion will begin with a streamlined explanation of the essentials of plastic extrusion. This will be adhered to by a failure of the procedure thoroughly and an expedition of methods to boost the efficiency of the extrusion technique

Understanding Plastic Extrusion Essentials
In the world of manufacturing, plastic extrusion stands as a basic procedure, important in the production of a multitude of daily things. At its core, plastic extrusion involves transforming raw plastic material right into a constant profiled shape. This is accomplished by thawing the plastic, frequently in the form of pellets or granules, and compeling it via a shaped die. The resulting item is a lengthy plastic piece, such as a pipeline, panel, or cord covering, that retains the shape of the die. This cost-effective approach is highly flexible, able to develop intricate shapes and suit a wide range of plastic materials. Basic understanding of these essentials permits for additional exploration of the a lot more intricate facets of plastic extrusion.
Thorough Extrusion Refine Break Down
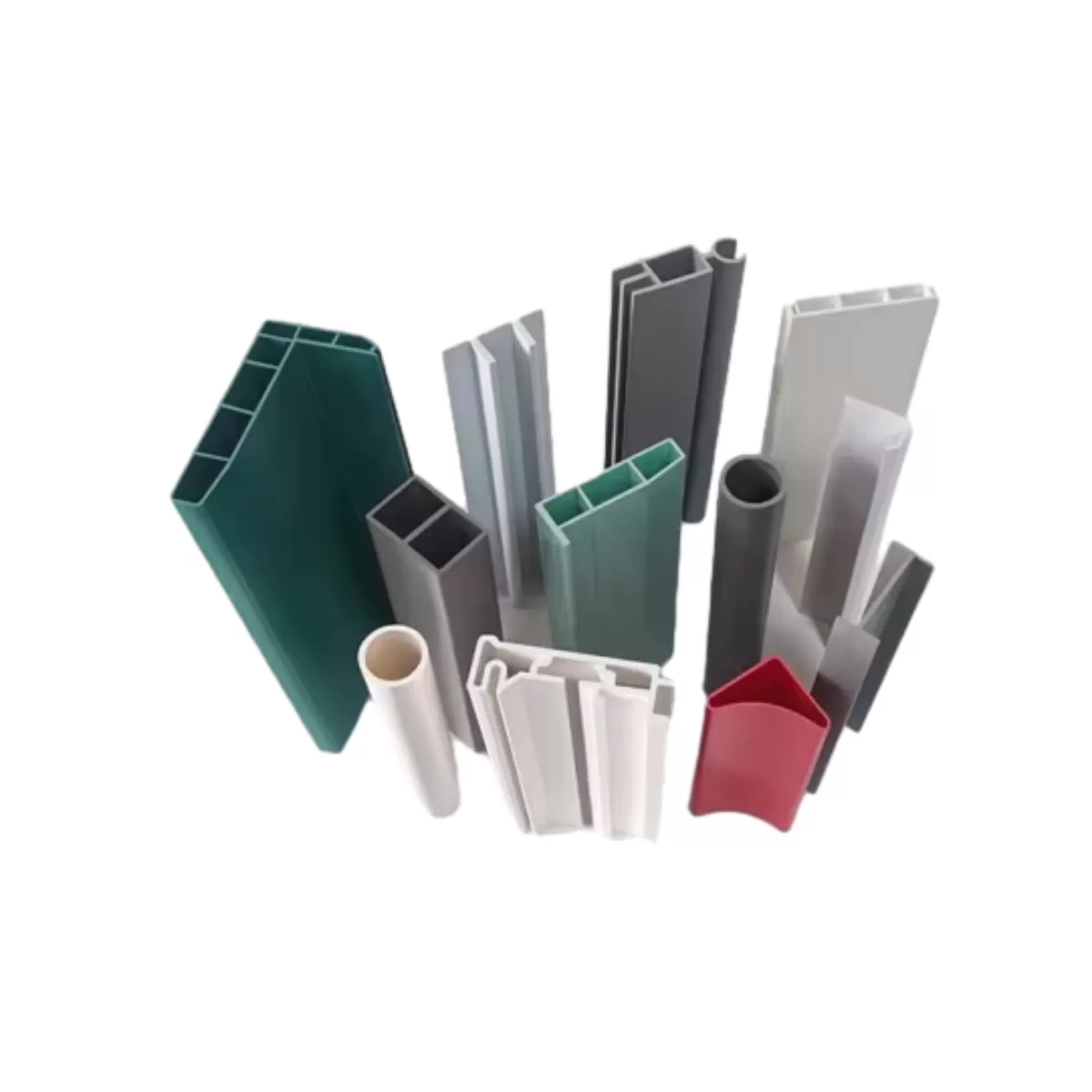
Improving Extrusion Method Efficiency
Performance gains in the plastic extrusion procedure can dramatically influence both the high quality of the end product and the general efficiency of the procedure. Continual optimization of the extrusion strategy is critical to keeping an affordable side. Methods that improve efficiency typically entail specific control of temperature level and stress throughout the procedure. Modern technologies, such as electronic systems and sensing units, read the article have actually been critical in achieving this control. The use of high-quality raw materials can lower waste and boost outcome quality. Normal upkeep of extrusion tools can additionally lessen downtimes, hence raising efficiency. Ultimately, embracing lean manufacturing principles can help remove unnecessary action in the process, advertising efficiency gains.
Just How Modern technology Is Changing the Face of Plastic Extrusion
The advent of new modern technology has significantly changed the landscape of plastic extrusion. It has actually brought about the development of advanced extrusion machinery, which has actually enhanced the efficiency and top quality of the plastic extrusion procedure. Technologies in the extrusion process have also been driven by technological improvements, providing improved abilities and flexibility.
Advanced Extrusion Machinery
Reinventing the world of plastic extrusion, advanced equipment imbued with innovative modern technology is ushering in a brand-new age of effectiveness and accuracy. These equipments, equipped with cutting-edge attributes like self-regulating temperature level control systems, make sure ideal conditions for plastic handling, thus decreasing waste and improving product top quality. High-speed extruders, as an example, amplify result rates, while twin-screw extruders supply remarkable blending abilities, vital for developing click to investigate complex plastic blends. In addition, electronic control systems supply unmatched accuracy in operations, lowering human error. These devices are made for longevity, reducing downtime and upkeep costs. While these innovations are already exceptional, the continuous development of modern technology promises also better leaps ahead in the area of plastic extrusion machinery.
Technologies in Extrusion Procedures
Harnessing the power of contemporary innovation, plastic extrusion procedures are going through a transformative transformation. Advancements such as computerized numerical control (CNC) systems now allow for more accuracy and uniformity in the manufacturing of extruded plastic. Automation better boosts performance, lowering human mistake and labor expenses. The combination of man-made intelligence (AI) and device understanding (ML) formulas is revolutionizing high quality control, anticipating discrepancies, and enhancing the overall efficiency of extrusion procedures. With the introduction of 3D printing, the plastic extrusion landscape is also expanding right into brand-new realms of opportunity. These technical innovations are not just enhancing the high quality of extruded plastic products yet additionally driving the market towards a much more sustainable, efficient, and innovative future.
Real-World Applications of Plastic Extrusion
Plastic extrusion, a versatile and effective procedure, locates use in plenty of real-world applications. The automotive industry also harnesses this innovation to create parts like plastic and trim sheet. The stamina and versatility of plastic extrusion, combined with its cost-effectiveness, make it a crucial procedure throughout numerous markets, highlighting its prevalent useful applications.
The Future of Plastic Extrusion: Trends and predictions
As we look to the horizon, it comes to be clear that plastic extrusion is poised for substantial developments and improvement. Eco-friendly options to traditional plastic, such as bioplastics, are likewise anticipated to acquire grip. These trends suggest a vibrant, developing future for plastic extrusion, driven by technical innovation and a commitment to sustainability.
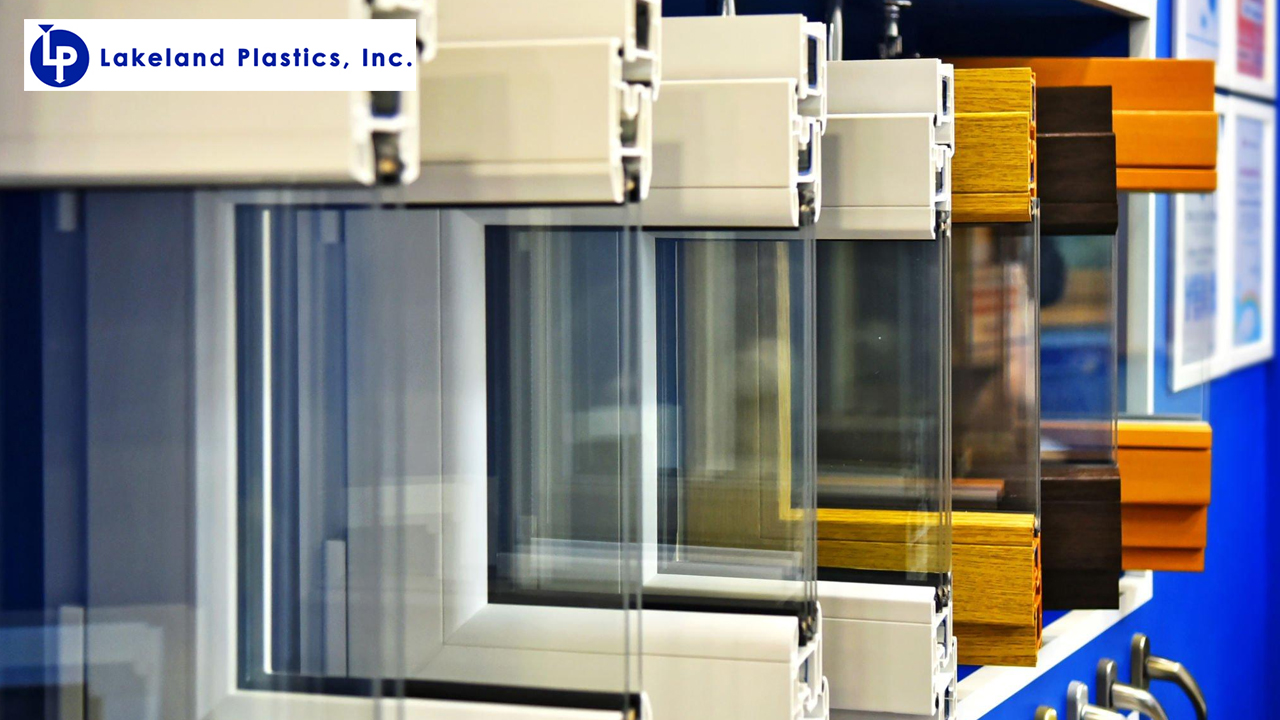
Verdict
In conclusion, plastic extrusion is a complex process that utilizes advanced technology and varied products to develop varied items. As plastic production continues to develop, it remains an important part of many industries worldwide.
In significance, plastic extrusion is a high-volume manufacturing procedure in which raw plastic material is melted and formed right into a continual account.While plastic extrusion is a frequently here are the findings utilized method in manufacturing, the products made use of in this process significantly influence its last result. At its core, plastic extrusion includes transforming raw plastic product right into a continuous profiled form. It has actually led to the advancement of advanced extrusion equipment, which has actually enhanced the performance and top quality of the plastic extrusion process.In conclusion, plastic extrusion is an intricate process that utilizes innovative innovation and varied products to create varied products.